Nel numero di settembre della rivista Automazione Integrata è stato affrontato il tema delle Tecnologie Green.
Questo focus ha proposto una panoramica delle opinioni dei player dell’automazione e del controllo sulle attuali possibili strategie di manutenzione degli asset produttivi e sull’adesione delle aziende al supporto ottenibile dalle nuove tecnologie.
Qui l'intervista a Andrea Pozzi, Chief Technology Officer di Tecnomotion del Gruppo Mondial
Manutenzione, il punto della situazione
Quali politiche di manutenzione sono principalmente adottate?
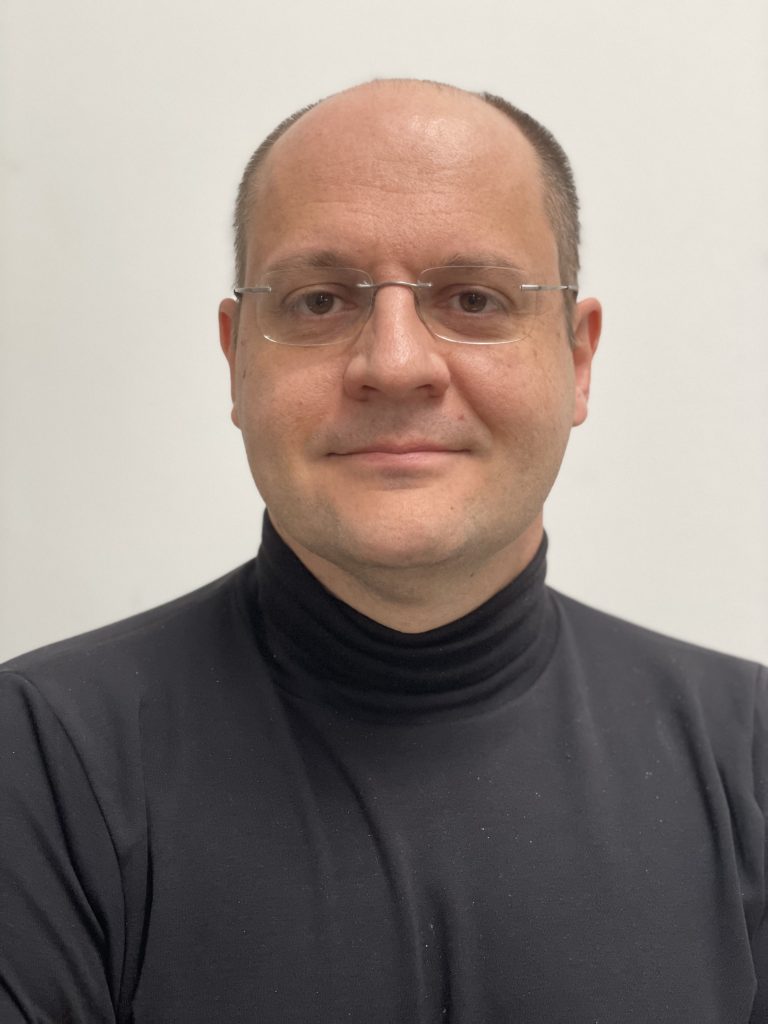
Solitamente ci si attiene a quanto è scritto nel manuale dell'impianto, e si pianificano manutenzioni periodiche. La policy più adottata è la manutenzione ordinaria, con una serie di controlli di lubrificazioni, dei giochi, tensionamento delle cinghie, precarichi dei cuscinetti etc. Si schedulano gli interventi e si inseriscono nel piano di manutenzione dello stabilimento. Quindi al momento dell'acquisto dell'impianto si definiscono già i futuri step della manutenzione programmata.
Negli ultimi tempi, c'è una crescente attenzione verso la manutenzione predittiva. Come Gruppo Mondial, stiamo proponendo ai clienti una serie di sistemi hardware e software, che permettono di misurare nel tempo il degrado degli asset e attraverso allarmi non bloccanti, segnalano la necessità di intervento. Questo approccio presenta una duplice sfida:
In funzione della complessità dell'impianto può essere difficile monitorare l'evoluzione dei parametri. Gli algoritmi si basano sulla misura di condizioni fisiche e quando c'è un impianto molto complesso con tanti asset, inserito in una linea articolata, in un ambiente rumoroso, andare a discriminare i segnali dei singoli asset, rende complesso disaccoppiare le problematiche.
Vi sono evidenti differenze tra grandi, medie e piccole aziende, e anche tra tipologie diverse di processi produttivi? Qual è secondo voi l’approccio migliore?
Le differenze tra piccole, medie e grandi aziende sono evidenti. Le aziende con grandi produzioni di serie e strutture organizzate, trovano più facile implementare la manutenzione predittiva grazie alla comparabilità degli impianti. Tipicamente, in una mass-production la struttura produttiva è ridondante, con diversi impianti che eseguono le stesse lavorazioni: è più facile schedulare un fermo semplicemente riprogrammando la produzione sulle diverse linee.
Nelle aziende con impianti in quantità più limitata, il fermo è più oneroso e difficile da programmare, col rischio di posticipare, e arrivare al breakdown. La manutenzione predittiva, tramite segnali di warning avvisa del logoramento prima che ci sia un impatto sulla qualità della produzione. È il sistema più efficiente in quanto si interviene solo a fronte di una reale esigenza e c’è un margine per pianificare l'intervento. Ignorare l’allarme rischia di sfociare nel fermo impianto, con i costi gravosi di perdita di produzione netta, oltre al rischio disponibilità ricambi.
Le tecnologie per la manutenzione
AI, IoT, Cloud Computing, smart sensor, edge computing, e quant’altro: quale il contributo alla manutenzione? Tra le aziende del vostro mercato di riferimento vi sono casi che si possono definire di eccellenza per la gestione della manutenzione degli asset produttivi?
L’AI è cruciale per isolare i segnali rilevanti in sistemi complessi, riesce a discriminare, a fronte di una quantità enorme di dati, le correlazioni che poi generano i guasti, e definire le soglie di preallarme.
Il cloud computing, nonostante le sue potenzialità, soffre di una percezione negativa sulla sicurezza dei dati. Tantissime soluzioni si basano su cloud, ma nonostante le garanzie sull'anonimizzazione dei dati sensibili, molte aziende temono possa essere rischioso far comunicare l’impianto con un cloud esterno, condividendo dati sulla produzione.
Per questo l'Edge Computing, che elabora i dati localmente senza trasmetterli all'esterno, è preferito per la sua percezione di maggiore sicurezza. Anche gli Smart Sensors, dotati di intelligenza propria, possono comunicare direttamente con il cloud. Ma la mancanza di integrazione tra diversi sistemi cloud può complicare la manutenzione. Se ci sono varie applicazioni tecnologiche che si sovrappongono, si generano diversi cloud distinti. La sovraproduzione di dati che non dialogano, rende più complessa la manutenzione.
“L’approccio integrato è più efficace per gestire i dati provenienti da impianti complessi. Il cloud ha enorme potenzialità, è sicuramente una soluzione migliore. Deva esserci maggiore fiducia nei confronti di chi ha in gestione i dati. Così come si ha fiducia nella propria banca, che gestisce i dati del proprio conto corrente. Si tratta di una questione culturale che si risolverà nel tempo.".
Andrea Pozzi, Chief Technology Officer di Tecnomotion del Gruppo Mondial
Il supporto al mercato
Con quali soluzioni supportate le aziende nell’implementazione di strategie di manutenzione coerenti con le esigenze di una Smart Factory?
È un po' la scommessa identitaria vincente del Gruppo Mondial che con Tecnomotion e Smart Factory si propone come partner unico in grado di fornire soluzioni chiavi in mano che rappresentano lo stato dell'arte in termini di affidabilità e interazione con il resto dell'impianto.
Come Gruppo, forniamo soluzioni integrate ed efficienti, che riducono la complessità lato cliente, al minimo indispensabile, e minimizzano falsi positivi, anche in presenza di sistemi molto complessi come quelli che noi forniamo abitualmente.