- Quali sono le principali problematiche di processo che si vogliono risolvere con l’automazione?
- In ambito confezionamento e imballaggio, quali sono le soluzioni di automazione più richieste?
- Per quanto sia difficile generalizzare, stante l’estrema varietà di possibili soluzioni impiantistiche, quali sono le principali caratteristiche che soluzioni innovative per il packaging devono avere per ottenere il gradimento del mercato?
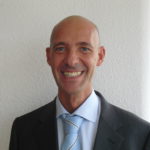
I processi di confezionamento e imballaggio sono trasversali rispetto a una molteplicità di settori industriali, i principali tipicamente collegati al mondo del consumo: alimenti, farmaci, elettronica, editoria, giochi…Il packaging ha assunto ruoli aggiuntivi rispetto alla sola funzione di contenitore del prodotto: sottolinea e differenzia il marchio, contiene informazioni aggiuntive sul contenuto, arricchisce e completa le funzionalità dell’oggetto. I produttori che operano in queste tipologie di mercato hanno beneficiato, nel corso degli anni, di soluzioni di automazione sempre più sofisticate, anche grazie alle risposte che gli OEM hanno saputo dare alle loro principali esigenze. Nel corso degli ultimi anni, il settore del consumo ha subito pesanti trasformazioni e l’automazione ha saputo assecondare le nuove richieste. Un primo aspetto critico è quello legato ai volumi produttivi, soggetti a forti variabilità nel tempo, sia positive che negative (come abbiamo imparato in questi ultimi anni). Le macchine per l’imballaggio devono avere la flessibilità per garantire efficienza rispetto alle diverse situazioni di mercato, considerando che i prodotti di cui stiamo parlando vengono gestiti per la maggior parte "just in time". Si tratta di garantire, da un lato, produttività in presenza di una forte domanda, dall’altro di assorbire inefficienze (sottoimpiego di personale e macchinari) in presenza di una domanda debole. Qui ci si collega direttamente ad altre due esigenze particolarmente avvertite in ambito imballaggio, ovvero quella di gestire un considerevole numero di varianti di un prodotto base o di un packaging esterno. Gli OEM sono dunque chiamati a progettare macchine che possano operare su di un ampio mix produttivo, che abbiano tempi di setup contenuti e che possano essere adattate in modo semplice ed economico a future evoluzioni e riprogettazioni del prodotto finito o del suo contenitore. Infine, un argomento nuovo e interessante riguarda gli aspetti che si richiedono ai sistemi di automazione in termini di integrazione con i sistemi informativi aziendali o, comunque, in tema di caratteristiche sempre più spinte verso la raccolta dati e il networking tra macchine. Oltre a intervenire sul processo puro, l’automazione gioca sempre più un ruolo fondamentale anche nel rispondere a problematiche collegate alla tracciabilità del prodotto, alla gestione dei dati di produzione e alla manutenzione preventiva. Quanto sopra ricordato, insieme ad altri aspetti trascurati in questa rapida disamina ma importanti per definire le performance dei macchinari richiesti dai produttori (in primis il prezzo che l’utente finale è disposto a riconoscere nell’acquisto della macchina), ha un impatto diretto sulle caratteristiche che i costruttori richiedono ai sistemi di controllo e di "movimentazione" che governano i processi di confezionamento/imballaggio. Non a caso abbiamo parlato di "movimentazione": in generale, il 20% dei sistemi Motion Control commercializzati viene in qualche modo impiegato in applicazioni legate al mondo del packaging. Le funzionalità di un controllore Motion sono infatti direttamente collegate alla flessibilità dei formati e alle velocità di processo. La possibilità di sincronizzare in modo semplice e preciso i diversi assi di movimentazione presenti sulla macchina, utilizzando profili di camma definibili e modificabili elettronicamente e non meccanicamente, si è per esempio rivelato uno strumento fondamentale per portare innovazione nella concezione delle macchine per il confezionamento. Nella direzione della flessibilità produttiva, ma anche in risposta all’esigenza di assorbire senza costi economici e sociali le fluttuazioni della domanda o a quella di manipolazione ripetitiva o "igienica" in determinati settori, si orienta l’impiego sempre più importante di robot all’interno delle fasi di imballaggio primario e secondario, spesso in associazione a sistemi di visione. Le performance che vengono richieste ai sistemi di Motion Control e robotica ha portato molti costruttori e utenti finali a considerare in modo diverso la disponibilità delle soluzioni presenti sul mercato: si preferiscono sempre più spesso soluzioni integrate di un unico fornitore, piuttosto che la combinazione di diverse piattaforme, arrivando spesso non solo a ottenere migliori prestazioni (obiettivo principale) ma anche a ottimizzare il costo complessivo dell’architettura selezionata (in termini di progettazione, programmazione, tempi di start up, ricambi e gestione interna). In relazione a queste considerazioni, Mitsubishi Electric è sempre stata all’avanguardia nella proposta di architetture di controllo integrate. L’ultima evoluzione disponibile, iQ Platform, utilizza una piattaforma multiprocessore in grado di combinare il controllo di sequenza (PLC), con il mondo del Motion Control e con CPU per il controllo di robot SCARA o antropomorfi, sempre di produzione Mitsubishi Electric. A sua volta, l’ambito Motion deriva da un matrimonio perfetto tra l’intelligenza del processore installato sulla piattaforma iQ e i muscoli dei servoazionamenti (oggi la generazione MR-J4), in comunicazione tra loro su rete a fibra ottica a 300 MBaud. Il processore governa le movimentazioni (sincronismi, camme elettroniche, master reali e virtuali, letture di tacche, interpolazioni…) mentre i drives si occupano al meglio del controllo dei motori, equipaggiati con encoder da 22 bit. Negli ultimi anni, iQ Platform si è arricchita inoltre della possibilità (tramite una scheda denominata MES-IT), di trasferire dati in real time direttamente all’interno di database residenti su PC. L’affidabilità di questa soluzione, basata su un sistema operativo Vx Works e in grado di fare back up di dati in caso di mancanza rete, fornisce uno strumento molto potente ai costruttori di macchine e agli utilizzatori: i primi possono fornire una soluzione completa ai propri clienti; i secondi sono in grado di realizzare, anche in autonomia, una completa integrazione dei macchinari con il sistema gestionale, gestendo al meglio l’incrocio tra la domanda e la produzione, tenendo sotto controllo l’efficienza degli impianti e gli aspetti di tracciabilità del prodotto.
Un sistema potente, affidabile con prestazioni uniche
Mitsubishi Electric, realtà mondiale nell’automazione industriale, mette a disposizione la propria grande esperienza di soluzioni in ambito Motion Control con schede assi, CPU Motion e servosistemi proponendo così sul mercato un sistema potente, affidabile con prestazioni uniche. Infatti i moduli Simple Motion per PLC serie L e Q e le CPU Motion QDS sono soluzioni che integrano funzioni avanzate di controllo del movimento come posizionamento, controllo di velocità, controllo di coppia, camme elettroniche, sincronizzazione assi, rilevamento tacche. La comunicazione tra CPU Motion e servo MR-J4 avviene tramite il motion-bus in fibra ottica SSCNET III/H che permette di raggiungere velocità pari a 300Mbps (150Mbps in full duplex). Grazie al collegamento in fibra ottica, è inoltre possibile raggiungere distanze fino a 1600 metri tra i dispositivi. La soluzione Simple Motion mette a disposizione dell’utente, funzioni con una programmazione semplificata e intuitiva risolvendo applicazioni motion di alto livello senza la necessità di essere esperti nell’utilizzo di complicati software di programmazione. L’architettura del sistema Motion Mitsubishi permette di controllare fino a 96 assi sincronizzati impiegando un unico rack, mentre con sistemi mutli-rack è possibile arrivare a controllare fono a 1280 assi. I “muscoli” del sistema sono i servo di ultima generazione MELSERVO MR-J4 che permettono quindi all’intero sistema di esaltare la produttività e le prestazioni mantenendo un elevato standard di sicurezza. MR-J4 con una banda passante pari a 2,5kHz, si distingue per le alte performance e funzionalità anche nelle applicazioni più complesse, idoneo in tutte le applicazioni di motion control con particolare attenzione ai settori del confezionamento, assemblaggio e manipolazione. Integra di serie un’ampia gamma di funzioni user-friendly in grado di minimizzare i tempi di sviluppo e le complesse operazioni di start up, garantendo perfetta armonia tra la meccanica e l’elettronica. Gli amplificatori sono dotati di serie dell’innovativa “life diagnosis function” la quale controlla lo stato dei componenti interni installati, come i condensatori e i relè, informando l’utilizzatore sull’eventuale deterioramento di tali componenti. In termini di funzioni dedicate alla sicurezza MR-J4 integra di serie l’ingresso STO (Safe torque Off) su tutte le serie di servo amplificatori e tramite un modulo opzionale è disponibile la funzione SS1 (Safe Stop) in accordo con la normativa EN61800-5-2. Il sistema supporta gli standard di sicurezza SIL2 (EN62061) e PLd (EN13849-1).