Nelle imprese industriali non sono ancora molti i progetti di manutenzione predittiva avviati, ma tanti sforzi vanno in quella direzione. Sono applicazioni complesse che richiedono competenze multidisciplinari e, soprattutto, una profonda conoscenza dei macchinari. Analizziamo gli esordi, gli scenari e le strategie praticabili.
- La manutenzione: esordi e sviluppi
- Le fasi: prima comprendere, poi implementare
- La manutenzione come leva di competitività
- La manutenzione come safety
- Le competenze: servono quelle multidisciplinari
- Le principali strategie e gli scenari di manutenzione
La manutenzione: esordi e sviluppi
Per le aziende di produzione che basano la propria attività sui macchinari è fondamentale predisporre un piano di manutenzione per mantenere in buono stato di salute macchine e impianti al fine di evitare rotture e fermo macchina onerosi e gravosi, sia per i costi di riparazione del macchinario stesso sia per i danni potenziali causati da un blocco della produzione. Grazie alle tecnologie abilitanti di Industria 4.0, anche la manutenzione sta compiendo un salto tecnologico, in particolare con il modello predittivo.
Di manutenzione predittiva si fa un gran parlare. «È dagli esordi del 4.0 che si parla di manutenzione predittiva, un tema caldo, diventato quasi uno slogan adottato per dare l’idea, quasi l’illusione, sulla possibilità di avere macchine che non si guastano, capaci anche di autodiagnosticarsi e autoripararsi», ha detto Sergio Cavalieri, prorettore e professore ordinario del Dipartimento di Ingegneria Gestionale, dell’Informazione e della Produzione dell’Università di Bergamo, in occasione del webinar sulla Manutenzione Predittiva nell’Industria 4.0, promosso dal Competence Center Made e da lui moderato.
Ma non è così: le macchine si guastano e continueranno a guastarsi. L’obiettivo della manutenzione predittiva è, semmai, quello di mitigare gli effetti legati a una gestione della manutenzione non adeguata. Per questo è importante che si continui a parlarne, soprattutto in un’ottica di orientamento per le aziende.
Proprio l’orientamento, rivolto in particolare alle pmi, è una delle attività di Made per capire le varie declinazioni del 4.0, di cui la manutenzione predittiva è parte. Attività che, grazie alla realizzazione delle isole tecnologiche con la collaborazione di numerosi partner, tra i quali Celada con i suoi macchinari industriali e Brembo, che ha avviato un progetto di manutenzione predittiva (segue un’intervista dedicata), offre anche la possibilità di toccare con mano come una tecnologia applicata possa migliorare i processi all’interno di un’azienda.
Le fasi: prima comprendere, poi implementare
La manutenzione predittiva si basa sui dati, generati dai sensori o direttamente dalle smart machine. Oggi, l’Industrial IoT, tra le tecnologie chiave di Industria 4.0, permette di avere protocolli interoperabili e open source che consentono di ottenere dati più strutturati e in tempo reale. Con tali dati si costruisce un modello predittivo, che prevede l’intervento manutentivo evitando deterioramenti e fermi improvvisi. Modello che spesso si applica solo a un componente della macchina ritenuto critico.
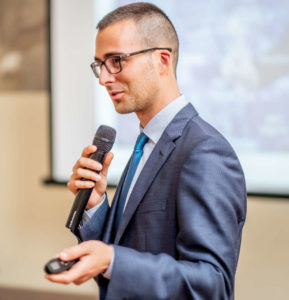
«La manutenzione predittiva è un vestito che si cuce su singoli componenti chiave di una macchina», ci spiega Francesco Sortino, responsabile Innovazione Gruppo R.F. Celada e membro del Comitato Tecnico-Scientifico di Made. «Esiste a piccole dosi su applicazioni sviluppate dal costruttore della macchina, perché per fare della manutenzione predittiva serve un modello dinamico del componente e serve comprendere come questo evolve nel tempo e nello spazio fisico con tutte le forze e le variabili di processo in gioco. È un’attività complessa perché non è sufficiente rilevare i dati e fare proiezioni delle evoluzioni, ma è necessaria una conoscenza approfondita dei dati, dei parametri fisici e delle leggi che li governano perché potrebbero anche avere delle progressioni non lineari. Ecco che per gestire queste informazioni bisogna avere una conoscenza approfondita del componente e del suo comportamento all’interno del sistema mentre è in opera. E questa conoscenza la può avere solo chi ha progettato e costruito la macchina».
Celada è un’azienda storica italiana da più di 80 anni con sede a Cologno Monzese (MI) e diverse subsidiary. È un distributore e integratore diretto di macchinari ad alta tecnologia e un costruttore di linee automatizzate, si occupa anche di retrofitting e revisioni. «Per rispondere alle richieste di una manutenzione sempre più avanzata abbiamo delle linee di investimento di R&D che vanno in quella direzione, ma prima di partire con un progetto bisogna stabilire se effettivamente ha senso strutturare un modello predittivo, poiché a volte un modello Cbm (Condition-based Maintenance) è già sufficiente».
«Esistono tanti sforzi da parte di aziende anche di grandi dimensioni per lavorare nella direzione della predittiva, ma il problema più grosso con il quale si scontrano è che la intendono a livello di impianto. Invece, la manutenzione predittiva ha senso solo se applicata a singoli componenti strategici - ad esempio, i cuscinetti di un mandrino perché quando iniziano a degenerare per usura causano disagi produttivi fino al fermo macchina - anche perché la mole dei dati da raccogliere per realizzare un modello efficace è molto alta».
La manutenzione come leva di competitività
L’evoluzione delle strategie manutentive ha portato a non considerare più la manutenzione come un puro costo. Oggi, con un’adeguata politica di manutenzione si può intervenire in maniera proficua all’incremento di diversi fattori che migliorano la produttività di un’azienda.
Di questo ha parlato Nicola Pietragalla, responsabile Tecnico e Cofondatore di Tesar, software house di Busto Arsizio (VA) specializzata nel mondo Industria 4.0, intervenendo al webinar sulla manutenzione predittiva e l’Industria 4.0 di Made. «L’efficienza è uno dei primi fattori interessati da una buona politica di manutenzione. Evitando fermate della produzione non programmate si ottimizza il piano di lavoro, migliorando l’indice Oee, l’Overall Equipment Effectiveness».
Buone politiche manutentive contribuiscono anche al miglioramento della qualità, perché permettono di mantenere in perfetto stato attrezzature e utensili e altri componenti che possono influire sulla precisione dei prodotti, e alla riduzione dei costi di produzione, perché evitando i fermi macchina si evitano i costi per la mancata produzione, i costi della manodopera inattiva e quelli per la riorganizzazione. Infine, si può ottenere anche un miglioramento dei tempi di servizio e di risposta al mercato, come diretta conseguenza dell’aumento dell’efficienza e un miglioramento della qualità.
La manutenzione come safety
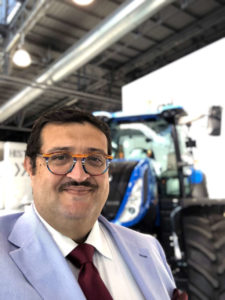
Un altro aspetto che non incide sulla produttività, ma che può essere migliorato da adeguate politiche di manutenzione è la sicurezza intesa come safety.
«La manutenzione non riguarda solo l’efficienza del macchinario, relativamente a evitare un fermo macchina con conseguente blocco della produzione, ma anche la sicurezza dei lavoratori», spiega Giambattista Gruosso, professore associato del Politecnico di Milano e direttore scientifico di Made.
«Si pensi, ad esempio, alla punta di un trapano automatico: un’eventuale rottura potrebbe causare problemi agli operatori sul campo». Ecco, quindi, che prevedere eventuali usure e rotture incide anche sui costi legati alla sicurezza dei lavoratori, cosiddetti “near miss”, cioè gli incidenti o infortuni mancati.
Le competenze: servono quelle multidisciplinari
«La manutenzione predittiva non è una soluzione preconfezionata, disponibile a scaffale», afferma Valerio Pesenti, Data Scientist del Consorzio Intellimech, nel suo intervento al webinar su come si realizzano modelli di manutenzione predittiva.
«È un progetto nel tempo che evidenzia molte complessità e richiede competenze multidisciplinari spesso non presenti all’interno dell’azienda. È consigliabile adottare un approccio metodologico standard e adattarlo alla singola situazione, patendo sempre dall’individuazione degli asset critici».
Di solito le aziende adottano un mix di politiche manutentive, a seconda della frequenza degli eventi di guasto, dell’impatto e del valore del componente in gioco. Nella realtà, non sono molti i casi di manutenzione predittiva, ma tanti sforzi vanno in quella direzione. Sicuramente nei prossimi anni si assisterà a un forte sviluppo di questa politica manutentiva, tendenzialmente applicata a singoli componenti strategici e critici per l’azienda.
Le principali strategie e gli scenari di manutenzione
Per gestire i vari asset all’interno di una fabbrica è possibile adottare politiche di manutenzione differenti. Francesco Sortino le ha ben illustrate nel corso del webinar organizzato da Made.
Reattiva | Intervento solo a seguito di guasti o fermi di produzione |
Preventiva | Regolarmente eseguita a intervalli regolari. Senza attesa di guasti |
Proattiva | Migliorativa. Aggiornamento dei componenti per migliorarne prestazioni e vita utile |
CBM (Condition-Based Maintenance) | Rilevazione utilizzo macchinari, comparazione target di usura e pianificazione |
Predittiva | Pianificazione delle attività sulla base di un modello dinamico del componente |
La politica di manutenzione più semplice è quella di tipo reattivo. In questo caso la manutenzione si basa sulla sostituzione di un componente a seguito di guasto. Non vi sono pianificazioni, si interviene solo al bisogno.
L’evoluzione di questo modello è la manutenzione preventiva, che si basa sulla conoscenza, anche non analitica, dell’intervallo del tempo di usura che ci si aspetta da un componente o da un asset. Definito l’asset, si stabilisce un intervallo di utilizzo che il componente potrà sostenere senza subire perdite di performance; raggiunto questo intervallo si procederà con un intervento di manutenzione per riportare il componente allo stato iniziale di utilizzo, si pensi, ad esempio, all’ingrassaggio delle guide.
Un modello più evoluto, che inizia a prendere elementi derivanti dal 4.0, è rappresentato dalla Manutenzione Proattiva, ovvero di tipo migliorativo. In questo caso si parte da un’analisi del sistema allo scopo di identificare le condizioni che potrebbero causare potenziali problemi e limitare la vita utile dell’asset. Una volta identificati gli elementi critici si procede con la sostituzione del componente individuato con uno dotato di miglior performance.
Con il modello Cbm (Condition-based Maintenance), si sfonda la porta del 4.0. La manutenzione si basa sulle condizioni di stato degli asset in funzionamento. Un esempio è la manutenzione consigliata sulle automobili in base al chilometraggio: il sistema misura un parametro che è il chilometraggio, lo riporta a quanto definito come valore di soglia dal costruttore ed emette delle notifiche per avviare una pianificazione dei tagliandi.
Proprio la pianificazione è uno degli elementi che contraddistingue il modello predittivo. Anche la manutenzione predittiva si basa sull’analisi dei dati che provengono dall’asset da manutenere - ad esempio i valori di vibrazione o i parametri fisici di processo quali temperatura o pressione. L’evoluzione di questi dati viene riferita a un modello dinamico del sistema che consente di risolvere problemi che si potrebbero avere nella determinazione del valore di soglia, che nel Cbm è definito dal costruttore delle autovetture, mentre nel caso della manutenzione predittiva è definito dal modello stesso.
La previsione della condizione di guasto avviene tramite questo sistema che consente di identificare l’inizio dei processi degenerativi prima che questi si manifestino in modo distruttivo sui componenti che si vogliono monitorare. Il modello predittivo prevede, dunque, l’intervento manutentivo evitando deterioramenti e fermi improvvisi. La strategia manutentiva è da valutare in base a diversi fattori. Non sempre, infatti, è necessario ricorre a un modello predittivo, quando può essere valutato un sistema non reattivo come il Cbm.