C’è sempre più Industria 4.0 in Luna Rossa AC75, la nuova imbarcazione sviluppata grazie a sistemi di modellizzazione avanzatissimi che hanno stracciato i tempi tra progettazione e validazione e hanno contribuito a portarla in finale. Inoltre, alcune componenti in titanio sono state realizzate con stampa additiva: il racconto del fornitore tecnologico Altair Italia.
Da Ferrari a Luna Rossa, passando per Cimbali, Rimac e molte altre realtà nel mondo delle tecnologie avanzate. Negli uffici di Torino di Altair si fa innovazione 4.0, con creazione di complessi modelli di simulazione, high performance computing (HPC), Data Analytics e il migliore sfruttamento delle potenzialità dell’additive manufacturing di precisione. La collaborazione con il team di ingegneri di Luna Rossa Prada Pirelli inizia nel 2017 e, dopo due anni di intenso lavoro, si può ben dire che ci sia sempre più Industria 4.0 nello scafo della nuova imbarcazione AC75 Luna Rossa, che ci sta facendo sognare nelle acque della Nuova Zelanda per la 36ma America’s Cup.

«La vera sfida del nostro intervento è stata quella di riuscire a simulare con un’altissima capacità di approssimazione un corpo deformabile, lo scafo, nel contatto con un fluido, l’acqua, con tutte le variabili coinvolte come l’urto sull’onda ad alta velocità e i carichi che ne conseguono. Di conseguenza, tutte le simulazioni sul dimensionamento dello scafo e la scelta dei materiali hanno dovuto tener conto di questa complessità per consentire di trovare la massima leggerezza e il posizionamento ottimale del centro di gravità dell’imbarcazione», racconta Andrea Benedetto, managing director di Altair Italia, società tecnologica globale quotata al Nasdaq, che fornisce soluzioni per lo sviluppo prodotto, high performance computing (HPC) e Data Analytics.
Per ottimizzare il comportamento strutturale della barca, Altair ha fornito i software, ha affiancato i propri ingegneri al team di Luna Rossa e ha sviluppato una serie di personalizzazioni di tool finalizzate a velocizzare lo sviluppo della barca, accorciando al massimo i tempi tra la progettazione dello scafo in fibra di carbonio, la realizzazione e la validazione. Il tempo era infatti una condizione fondamentale da minimizzare, complici anche i rallentamenti imposti dalla pandemia.
«È stato necessario ricorrere a moltissima simulazione perché i tempi a disposizione per provare e correggere erano estremamente ridotti. Si trattava infatti di una architettura nuova, sviluppata in due fasi: la prima, con la barca 1, vero e proprio laboratorio d’innovazione sviluppato virtualmente, su cui validare tutte le ipotesi, correlare i dati, identificare le modifiche e le implementazioni da riversare poi sulla barca 2, varata direttamente in Nuova Zelanda», spiega Benedetto.
Partiti da una prima fase di ottimale dimensionamento della struttura, si è poi passati alla simulazione dei sistemi, tra cui la parte idraulica cui si è applicata la simulazione di dettaglio ai singoli componenti per la loro ottimizzazione, con importanti riduzioni di peso (anche del 20-30%) rispetto alle ipotesi iniziali di progetto, grazie a materiali compositi e alla stampa 3D in titanio di alcuni elementi.
«In pratica abbiamo applicato a Luna Rossa la nostra logica progettuale: ottimizzare la geometria in base alle prestazioni che vogliamo ottenere. Ovviamente la gestione sistemica della barca era in capo al team di ingegneri di Luna Rossa, noi li abbiamo supportati con i nostri strumenti per creare le geometrie ottimizzata», precisa il manager di Altair. Ma l’apporto di Altair alla stampa 3D va anche oltre: con gli stessi strumenti di simulazione modella la tecnologia produttiva, ossia simula il processo produttivo fino a generare le istruzioni del file da consegnare alla macchina per la produzione.
Altair e il modello ottimale di Rimac
Anche con Rimac, la super car elettrica realizzata in Croazia, Altair Italia ha battuto sui tempi il mercato: grazie ad accurate simulazioni di progetto e prototipi digitali, sono stati compressi tutti quei passaggi di verifica in laboratorio con i “crash test”, gli impatti reali per arrivare alla validazione dell’autovettura.
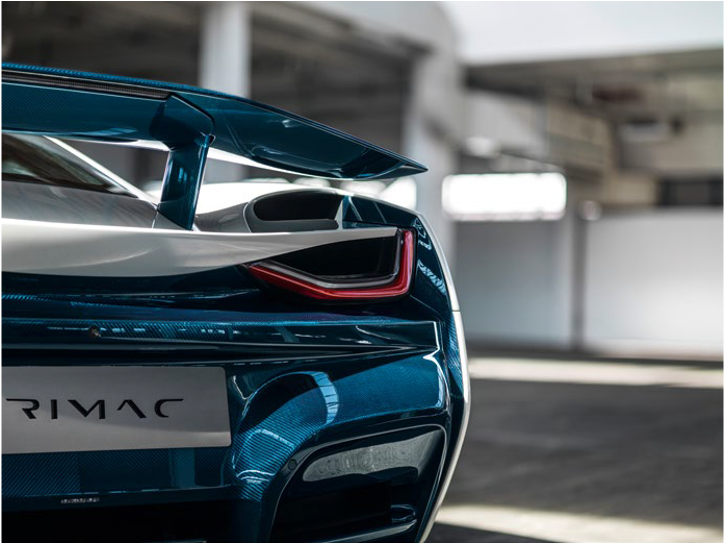
«Anche in questo caso abbiamo evitato “incidenti di percorso” ed è bastato un solo prototipo fisico per arrivare alla validazione finale», commenta Benedetto, un passato lui stesso nel mondo dell’automotive. Anche questa volta, con Rimac, hanno fatto la differenza la velocità di esecuzione del progetto, l’accuratezza delle simulazioni realizzate con ingegneri esperti in modo da guidare il progetto, a convergenza, verso il modello ottimale. «La simulazione è infatti il modo più veloce e meno costoso per individuare le soluzioni migliori in modo controllato, ripetibile ed efficiente, senza la costruzione di prototipi e senza eseguire test costosi», precisa Benedetto.
Altair modella anche le macchine Cimbali
In attesa del vincitore finale di America’s Cup tra Luna Rossa e il team New Zeland, Altair è impegnata anche nel supporto alla creazione della nuova generazione di macchine professionali per il caffè Cimbali: progettate in chiave 4.0, connettibili tra loro secondo il nuovo modello di business as a service (per servizi e manutenzione).
Altair per ora si è occupata di realizzare la modellizzazione virtuale delle nuove macchine, passo fondamentale nella realizzazione del “digital twin” nel momento in cui i dati rilevanti raccolti dal campo verranno convogliati nel sistema, riprodotti per “osservare” il comportamento delle macchine e interpretati per intervenire con azioni correttive e migliorative sulle macchine e i processi.
Altair è attiva anche nel mondo della data analytics e dell’ AI grazie a importanti acquisizioni, che sono state organicamente inserite all’interno di un portfolio di prodotti tecnologicamente avanzato.