L’ IoT nei processi manifatturieri è una realtà sempre più diffusa, ma ormai l’Internet delle cose è la base fondante anche di diverse tecnologie che nella vita di tutti i giorni ci sembrano scontate. Si pensi, ad esempio, allo shopping on-line e alla facilità con la quale ci si registra alle varie piattaforme, oppure alla possibilità di monitorare le prestazioni sportive attraverso dispositivi indossabili come gli orologi. In modo trasparente all’utilizzatore, l’IoT permette di rilevare, tracciare e misurare evoluzioni di parametri o transazioni, grazie allo scambio di dati e informazioni tra i vari oggetti.
Ogni ambito è dunque impattato dall’IoT, un mercato che in Italia vale 6,2 miliardi di euro e che vede tra i segmenti in maggior crescita quello industriale, definito Industrial IoT.
Secondo l’Osservatorio Internet of Things della School of Management del Politecnico di Milano, le applicazioni più diffuse sono quelle per la gestione della fabbrica (Smart Factory, 51% dei casi), impiegate soprattutto per il controllo in tempo reale della produzione e la manutenzione preventiva e predittiva, seguite dalle applicazioni per la logistica (Smart Logistics, 28%), dedicate alla tracciabilità dei beni in magazzino e lungo la filiera, e dallo Smart Lifecycle (21%), con progetti che puntano a migliorare le fasi di sviluppo di nuovi prodotti. E proprio di Industrial IoT e di protocolli per lo scambio dei dati nei processi manifatturieri ha parlato Francesco Sortino, responsabile Innovazione Gruppo R. F. Celada e membro del Comitato Tecnico-Scientifico del Competence Center Made di Milano, in occasione di un webinar sull’IIoT, promosso dal Made e dal Digital Innovation Hub (Dih) Lombardia e moderato da Davide Polotto, di cui riportiamo una sintesi dell’intervento.
Indice dei contenuti
L'IoT nei processi manifatturieri: la centralità del dato
Protocolli: dove applicarli e per quali utilizzi finali
Applicazioni IIoT nei processi manifatturieri: due esempi pratici
L’IoT nei processi manifatturieri: la centralità del dato
Alla base dell’IoT c’è il concetto di un insieme di oggetti in grado di sentire, trasmettere e condividere informazioni. Questi oggetti sono collegati tra di loro tramite reti pubbliche o private come Internet e reti locali. La rilevazione dei dati si basa, invece, sull’utilizzo di sensori o sulla generazione di valori logici da parte di unità di calcolo, che in ambito industriale posso essere i plc o i cnc. Per la trasmissione e la condivisione dei dati si sono definiti, a livello internazionale, vari protocolli di connessione, che definiscono le regole che governano lo scambio dei dati e framework di riferimento, che aiutano le aziende nella progettazione delle infrastrutture, definendo le classi di utilizzo dei dati stessi.
I dati sono, dunque, il cuore di questo concetto, che esteso alle fabbriche e al mondo industriale assume la denominazione di Industrial IoT e ha generalmente l’obiettivo di migliorare o controllare efficienze produttive, ridurre i costi e ottenere una migliore visibilità sui processi industriali. Secondo un Report di Boston Consulting del 2015 che definiva i nove pilastri di Industria 4.0, l’IoT è stato definito il collante, poiché tutte le tecnologie 4.0 si fondano sulla condivisione in real-time dei dati. L’IoT nei processi manifatturieri è dunque un asset fondante di Industria 4.0, la quale si realizza grazie alla presenza dei cosiddetti sistemi cyberfisici (Cps, Cyber Physical Systems), ovvero sistemi di calcolo connessi tra di loro e con il mondo fisico circostante. Si tratta di sistemi che condividono l’accesso e la gestione dei dati e che servono a “consumare” il dato generato dal campo. Applicazioni pratiche di questo concetto le troviamo, ad esempio, nei sistemi di monitoraggio o nell’ambito della progettazione, dove grazie alla creazione di gemelli digitali (Digital twin) si utilizzano i dati in relazione al modello digitale per favorire una progettazione più consapevole.
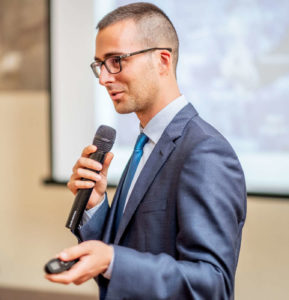
Protocolli: dove applicarli e per quali utilizzi finali
Il Piano Nazionale 4.0 mette al centro di tutto il dato e, tra i requisiti per ottenere gli incentivi, figura l’interconnessione dei dati con i sistemi informativi, tramite protocolli basati su standard di mercato, quali Tcp/IP, Http, Mqtt. Ulteriore requisito è che i dati provengano da un’identificazione univoca, ad esempio da un indirizzo IP. Emerge quindi la necessità di sviluppare architetture orizzontali e interoperabili, sia da un punto di vista normativo, sia sul fronte tecnico per consentire la scalabilità tra impianti industriali vasti e distribuiti. Nelle realtà di produzione dove prevalgono celle robotizzate, i protocolli più utilizzati sono quelli tipo Profinet, mentre salendo di livello i dati sono più strutturati e servono protocolli come MTConnect. Un altro aspetto che va sottolineato è l’importanza di estendere il beneficio dell’IIoT a tutto lo shopfloor, e non solo agli asset più recenti. A questo riguardo, è fondamentale distinguere tra impianti più moderni, dal 2016/2017 in poi, nei quali i costruttori hanno implementato nativamente i protocolli standard quali MTConnect e Opc UA, e quelli più datati, presenti in gran numero nelle nostre pmi, che richiedono di essere connessi tramite dispositivi Edge. Questi dispositivi rilevano solo certi tipi di dati, ma non per questo meno strategici.
Introducendo sistemi che svolgono Analytics e mettendo in relazione diversi parametri, si possono avere informazioni più approfondite che consentono di ottimizzarne l’efficienza. In questo caso i protocolli più comuni sono MTConnect, un protocollo open source basato su Http molto flessibile, ma monodirezionale, cioè con il limite che non può inviare informazioni esecutive alla macchina, e Opc UA, un protocollo bidirezionale che consente, invece, sia di ricevere informazioni dalle macchine sia di inviarle. Opc UA è un po’ più strutturato anche dal punto di vista della cybersecurity ed è più ampiamente diffuso laddove si fa controllo dei processi: ad esempio, nel campo delle macchine utensili consente di dare istruzioni alle macchine correggendo i parametri di usura degli utensili: si tratta di un sistema cosiddetto ad anello chiuso, che non richiede cioè l’intervento di personale. MTConnect è, invece, preferito per la Data Analytics, ad esempio per rilevare l’efficienza delle risorse produttive attraverso l’Oee (Overall Equipment Effectiveness).
Applicazioni IIoT nei processi manifatturieri: due esempi pratici
Due esempi concreti di applicazioni Industrial IoT riguardano un sistema di raccolta della conoscenza e un’applicazione di manutenzione intelligente.
La prima consente di storicizzare l’esperienza degli operatori delle macchine utensili. È un’applicazione utilizzata nelle imprese di produzione e in quelle manifatturiere che, attraverso una raccolta strutturata di dati, consente a nuovi operatori di avviare processi produttivi senza che sia necessaria una formazione specifica, con il valore aggiunto di non concentrare la conoscenza su pochi soggetti, una criticità molto sentita nelle imprese di produzione. In questo modo, a costo zero, si rende disponibile la conoscenza in modo più orizzontale.
Un altro esempio riguarda la manutenzione intelligente o predittiva. Misurando la variazione di parametri di processo - tramite modelli del macchinario o del sistema produttivo - è possibile modellare il comportamento, cioè tracciarne l’evoluzione nel tempo: quando si entra in aree di operatività rischiose o pericolose, che dal modello possono essere associate a condizioni di guasto imminente, può essere pianificata una manutenzione.
Il trend che si sta evidenziando da parte dei produttori va verso l’omogeneizzazione dei dati di processo su protocolli e architetture comuni. Accanto ai più accreditati MTConnect e Opc UA, si sta facendo strada Umati, in particolare nel settore macchine utensili.
Dai benefici fiscali alle potenzialità reali
«Dopo un primo approccio a Industria 4.0 motivato principalmente dai benefici fiscali, ora le aziende stanno comprendendo le potenzialità. E se inizialmente il focus era più concentrato sulla smart factory, ora si sta assistendo a un ampliamento dell’interesse lungo tutta la value chain. Tuttavia, manca ancora la capacità di fare Analytics per capitalizzare meglio i dati raccolti», è quanto ha affermato Giuseppe Linati di Digital Innovation Hub Lombardia, intervenuto al webinar Industrial Internet of Things dello scorso giugno, in merito all’attenzione delle imprese lombarde verso applicazioni IIoT. I Digital Innovation Hub sono organizzazioni di Confindustria che hanno lo scopo di accompagnare le imprese nel percorso di digital transformation, dialogando con le istituzioni da una parte - ad esempio con Made - e con le imprese, dall’altra, dando vita a un ecosistema sui singoli territori. «L’obiettivo è mettere a fattor comune competenze ed esperienze e renderle disponibili alle imprese», ha spiegato Linati. «Grazie a uno strumento messo a disposizione dal Politecnico di Milano è possibile misurare la maturità digitale delle imprese, che comprende anche la capacità di utilizzo e trasformazione dei dati». L’obiettivo è quello di definire una roadmap per migliorarla, aiutando le imprese a essere più competitive. Dih Lombardia agisce anche a livello internazionale essendo uno dei 30 Dih selezionati dalla Commissione Europea per aiutare le pmi a introdurre soluzioni di intelligenza artificiale».