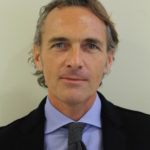
Quali sono le principali problematiche di processo che si vogliono risolvere con l’automazione?
I consumatori – sempre più esigenti – richiedono prodotti di alta qualità, a prezzi inferiori, e un assortimento molto vasto. Con questo presupposto, quello che è valido oggi potrebbero non esserlo domani. È una sfida che si combatte in parte sul prodotto vero e proprio e molto sul packaging. Chi fa impianti di confezionamento e imballaggio deve quindi pensare soluzioni molto aperte, affidabili ed efficienti per rispondere a esigenze che – in alcuni casi – non si sono ancora palesate.
In ambito confezionamento e imballaggio, quali sono le soluzioni di automazione più richieste?
Sicuramente efficienza e flessibilità; l’automazione deve migliorare la produzione rendendola al tempo stesso veloce e accurata.
È fondamentale avere cambio-formato rapidi e integrati e impianti che si adattano a prodotti differenti, nel minor tempo possibile, senza bisogno di modifiche meccaniche.
La capacità produttiva deve essere alta ma affidabile, quindi utilizzo massiccio di tecnologia per garantire prestazioni e controllo qualità.
Altro aspetto imprescindibile è l’attenzione ai costi: basso consumo energetico, riduzione dei prodotti non conformi (quindi da scartare!), automatizzazione della linea per ridurre il personale.
Per quanto sia difficile generalizzare, stante l’estrema varietà di possibili soluzioni impiantistiche, quali sono le principali caratteristiche che soluzioni innovative per il packaging devono avere per ottenere il gradimento del mercato?
A mio avviso avrà successo chi potrà garantire flessibilità e affidabilità a un giusto prezzo. La capacità di dimensionare gli impianti con un livello di automazione e tecnologia sufficiente, è la vera sfida. Ormai non esistono più missioni impossibili, dal punto di vista tecnologico, si tratta però di renderle sostenibili evitando inutili e dannosi over engineer.
Nuove tecnologie al servizio del Packaging
Come sempre al primo posto per l’innovazione apportata nel mondo tecnologico, SICK presenta DeltaPac, il più recente capitolo del suo ampio portfolio prodotti. Questo sensore consente di rilevare con estrema affidabilità oggetti che scorrono nei flussi di processo anche se sono tra loro adiacenti. Fino ad oggi, si rivelava necessario separare i pacchi che venivano sottoposti ad un processo di packaging. Tale separazione era fondamentale per contarli e controllarne il passaggio. La separazione tra i pacchi consentiva una comoda tracciatura, ad esempio, gestita con fotocellule a riflettore o con altre tipologie di sensori ottici. Purtroppo, questa soluzione è costosa e dispendiosa meccanicamente. Ed obbliga la progettazione di separatori meccanici che impongono un costante controllo manutentivo. Grazie all’innovazione apportata da DeltaPac, tali meccanismi possono essere relegati al passato. Questo è possibile grazie alla soluzione optoelettronica brevettata da SICK “Delta-S-Technology”.
Delta-S tecnologia brevettata
Delta-S-Technology trova la sua applicazione laddove esistono dei bordi da dover essere individuati. Si avvale di un potente emettitore dotato di quattro LED Pin-Point 2.0, che hanno un’energia di emissione paragonabile a quella di un laser, combinato con SIRIC una tecnologia ASIC brevettata da SICK. L'apparato di ricezione è in grado di comprendere, confrontando l’energia luminosa proveniente dal lato destro o sinistro del bordo, se il bordo stesso è stato superato o meno. È un sistema di ricevitori dunque progettato per valutare il differenziale luminoso attraverso il bordo che delimita un pacco dall’altro mentre essi transitano appaiati lungo il processo. Gli spigoli degli oggetti sono identificati in modo affidabile, anche quelli dotati di raggi superiori ai 2 mm fino ai 20 mm. DeltaPac è in grado di riconoscere anche il più piccolo cambiamento del bordo grazie a una delle sue caratteristiche principali, tre le quali l’alta precisione. È così possibile individuare fino a 200.000 pezzi all'ora e velocità fino a 3 m/s.
Vantaggi per i costruttori di macchine per il Packaging
DeltaPac apre nuove opportunità ai costruttori di macchine confezionatrici. Alcuni componenti macchina come i separatori meccanici non sono più necessari; questo comporta oltre ad un risparmio nei costi, anche ad un incremento dello spazio disponibile nella macchina. Inoltre, gli effetti positivi sono molteplici: durante il flusso di produzione le collisioni sono ridotte al minimo e sono sicuramente abbattuti i tempi di fermo macchina, il caricamento non corretto nei punti di raggruppamento e la perdita di qualità causata dall’urto tra oggetti. Il tutto si traduce in ottimizzazione del tempo, di energia e dell’efficienza della macchina confezionatrice stessa.
Configurazioni del sensore “su misura”
Le configurazioni “su misura” possono essere impostate velocemente e senza difficoltà. SICK ha cercato di mettere in atto le richieste dei produttori di macchine confezionatrici in termini di dispositivi preconfigurati. Installazione, connessione, rilevamento – l’utilizzatore non avrà alcun problema con le istruzioni operative. Le versioni Smart, se connesse in IO-Link, aiutano il cliente ad adeguare il funzionamento del sensore alle proprie esigenze.