Una singola pinza speciale realizzata in PA 2200 permette di ridurre i tempi di configurazione e aumentare l’efficienza della produzione, ottenendo al contempo una riduzione del peso di oltre il 70% (fonte: SSI Schäfer).
Immagazzinaggio, movimentazione e trasporto, prelievo degli ordini e altro ancora: SSI Schäfer è un’azienda specializzata nei sistemi modulari di stoccaggio e logistica e nel software associato. Per il processo di produzione dei contenitori per lo stoccaggio, il trasporto e il prelievo degli ordini, l’azienda era alla ricerca di un modo più conveniente e soprattutto più affidabile e agevole per estrarre i contenitori dalle proprie macchine di stampaggio a iniezione. La soluzione è stata offerta dal processo di Additive Manufacturing.
Dal problema...
Guasti di sistemi informatici, errori umani... l’elenco delle possibili cause di una perdita a livello di produzione è lungo. Forse meno emozionanti, ma ancor più rilevanti per le operazioni quotidiane rispetto agli scenari catastrofici, sono i problemi relativi ai processi intrinseci alla produzione.
Questo vale anche per SSI Schäfer: per molti anni, l’azienda ha utilizzato un sistema di prese in alluminio applicabile universalmente per produrre i propri contenitori per lo stoccaggio, la raccolta e il trasporto. Queste “mani metalliche” erano formate da profili in alluminio con alloggiamenti per ventose. Questo meccanismo veniva regolato per mezzo di viti esagonali, di continuo, a seconda del tipo di contenitore prodotto. Il fattore decisivo in questo caso è la precisione: le ventose devono essere esattamente nella giusta posizione affinché i contenitori possano essere rimossi dalla macchina di stampaggio a iniezione in modo semplice e veloce durante il ciclo di produzione. In caso contrario, il contenitore potrebbe inclinarsi, cosa che potrebbe comportare un arresto della produzione. Anche senza che si verifichi questa situazione, che rappresenta il “caso peggiore”, è chiaro che i costi ricorrenti per il riattrezzamento sono significativi:
“A causa della vasta gamma di prodotti che realizziamo, dobbiamo cambiare la configurazione su una delle nostre numerose macchine di stampaggio a iniezione circa tre volte al giorno”, ha spiegato Michael Zander, Head of Plastics Production di Neunkirchen/Siegerland (Germania).
Finora erano necessari circa dieci minuti solo per queste conversioni, a cui si aggiungevano le corrispondenti perdite di ricavi per via dei tempi di inattività delle macchine e della produzione. In considerazione di questo fatto, è facile comprendere l’esigenza da parte dell’azienda di migliorare il processo. C’era anche un altro motivo: con una soluzione migliore, sarebbe stato possibile ridurre i costi non solo indirettamente ma anche direttamente, di fatto con una drastica riduzione dei tempi di configurazione e dei tempi di fermo delle macchine di stampaggio a iniezione.
...alla soluzione
Con il supporto dei consulenti tecnici di EOS Additive Minds, il team di SSI Schäfer è stato in grado di acquisire competenze in un breve periodo di tempo e ha identificato specificamente questo potenziale di miglioramento: la pinza in alluminio, soggetta a errori, doveva essere sostituita da diverse pinze dedicate, ognuna delle quali adattata individualmente alle dimensioni e alle forme dei rispettivi contenitori. Queste pinze dovevano essere durevoli, veloci da sostituire e adattate in modo ottimale ai requisiti corrispondenti.
L’idea di fondo è simile a quella dello sport: un decatleta è senza dubbio un ottimo sportivo, ma gli specialisti nelle singole discipline in genere sono notevolmente superiori. In linea con questo approccio, EOS e SSI Schäfer hanno iniziato a lavorare al progetto.
La progettazione delle pinze adatte era relativamente semplice, in quanto tutti i dati sui contenitori erano disponibili internamente. Era anche importante lasciarsi alle spalle vecchi percorsi progettuali e sfruttare al meglio le particolari capacità della stampa 3D: l’integrazione nella pinza dei condotti dell’aria, che a propria volta costituiscono la base per il meccanismo di presa pneumatica per l’estrazione dei contenitori, è una delle specialità dell’Additive Manufacturing. Era inoltre necessario progettare i componenti in modo tale da armonizzare stabilità e funzionalità, a causa delle dimensioni compatte e del peso contenuto della pinza.
“In definitiva, un design di questo tipo è sempre un compromesso”, ha commentato Torsten Kosiahn, Toolmaking Manager. Grazie al suo profilo con proprietà bilanciate, il materiale PA 2200 selezionato per questo scopo ha dimostrato le proprie caratteristiche in migliaia di applicazioni: solido, rigido, resistente alle sostanze chimiche e durevole. Inoltre, consente un elevato livello di dettaglio e opzioni complete di post-elaborazione: in breve, è ideale per componenti funzionali e connessioni mobili. Le pinze sono state prodotte tramite un sistema EOS P 396.
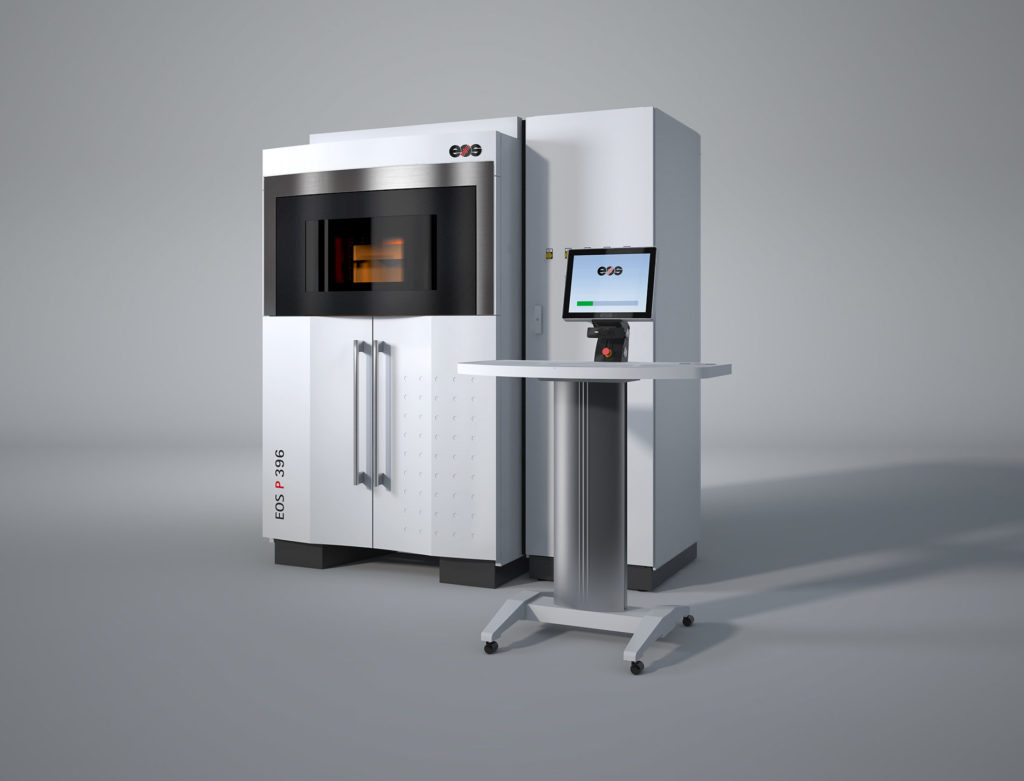
Un bilancio positivo
In questo modo, SSI Schäfer è stata in grado di progettare e costruire una moltitudine di pinze in pochi giorni. L’azienda ha inoltre ridotto drasticamente i tempi di riattrezzamento: bastano pochi clic per ottenere una pinza perfettamente abbinata al particolare contenitore. I risultati sono evidenti anche nelle cifre.
Questo approccio ha ridotto i tempi di configurazione dell’80% e ha permesso di guadagnare circa 120 ore di tempo di produzione all’anno. Difficilmente quantificabili in cifre sono le possibili spese consequenziali qualora un grave errore nell’impostazione della pinza dovesse portare a un guasto prolungato, perché con la messa a punto manuale delle pinze precedenti, il pericolo di errori operativi era sempre presente in background. Riprogettando le pinze di conseguenza, questo è praticamente impossibile: le ventose ora sono sempre nella posizione corretta. Le nuove pinze hanno anche un peso inferiore di oltre la metà rispetto a quelle precedenti grazie al materiale con cui sono realizzate. Questa riduzione di peso superiore al 70% e la maggiore facilità d’uso per l’utente sono naturalmente interessanti anche per il personale che effettua le conversioni. Tutti gli obiettivi di SSI Schäfer sono stati raggiunti: maggiore affidabilità, minori costi e peso ridotto, oltre che aumento della produttività.
“I nostri requisiti erano molto chiari: l’affidabilità e la velocità dovevano aumentare con la conversione delle pinze. Con la produzione tramite Additive Manufacturing dei nostri sistemi di prese, siamo riusciti a risolvere questo problema e a ridurre i costi. Sono molto soddisfatto del risultato e del supporto ottenuto dal team di EOS Additive Minds”, conclude Kasim Mohamed, Product and Innovation Manager, SSI Schäfer.