Per raggiungere una piena trasformazione digitale e sostenibile dell’industria, secondo il concetto del 5.0, si va verso l’integrazione delle tecnologie e delle piattaforme hardware e software che abilitano l’industria digitale.
I trend indicano, infatti, che da una parte la componente software è sempre più pervasiva, sia nella realizzazione di soluzioni meccatroniche sia nella gestione di tutte le fasi della vita del prodotto, dalla progettazione alla realizzazione, fino all’utilizzo in campo e all’assistenza.
Dall’altra parte, invece, si sta assistendo a un’evoluzione delle piattaforme di automazione e di meccatronica, proprio nel segno dell’integrazione.
Insomma, un mercato in trasformazione che Anie Automazione - che raggruppa le aziende fornitrici di queste tecnologie - monitora con un forum dedicato: il Forum Industria Digitale, nato dall’unione dei Forum Meccatronica e Software Industriale.
Proprio nel corso della prima edizione, che si è recentemente svolta a Cremona con l’organizzazione di Messe Frankfurt Italia, sono emerse le tendenze di un settore in costante evoluzione.
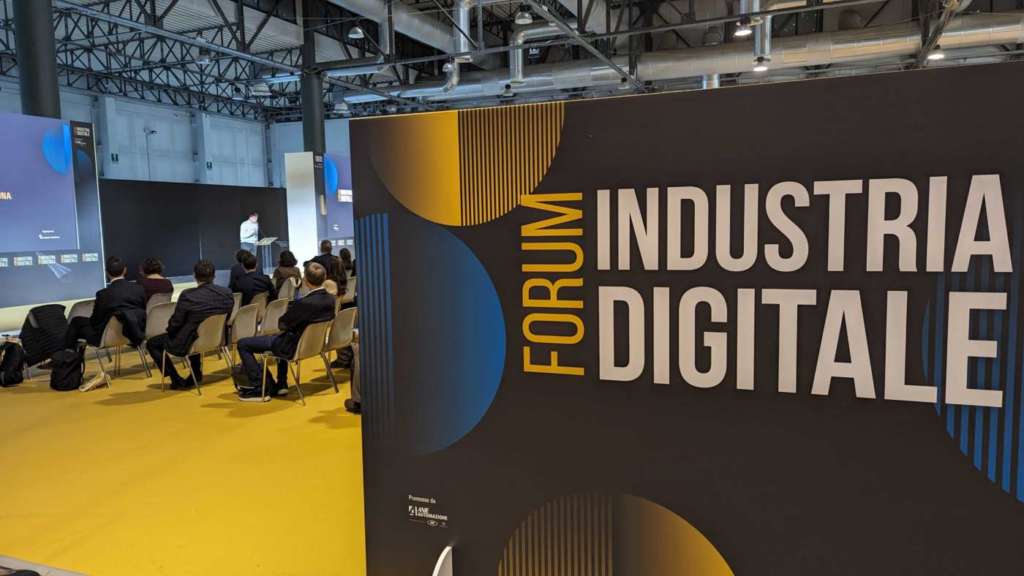
Cambia l’approccio meccatronico, supportato dalla potenza del software
La volatilità dei mercati e la necessità di reagire in modo veloce alle dinamiche di cambio requisiti e aspettative dei prodotti impone un nuovo approccio alla progettazione di macchinari e componenti meccatronici.
“Tecnologie quali il digital twin (gemello digitale) e l’intelligenza artificiale (AI) permettono di virtualizzare e simulare il comportamento di componenti e macchine, supportando progettisti e utilizzatori nel raggiungere una sempre maggiore affidabilità, velocità nel time-to-market ed efficienza”, ha affermato Sabina Cristini, Presidente Gruppo Meccatronica di Anie Automazione.
“Nello sviluppo di macchine e sistemi il software è ormai la componente base e saperlo gestire è diventata una sfida, in particolare nella confluenza delle Operational Technology, il regno dello shop floor e dell’automazione, con il mondo IT dei sistemi Erp e della gestione dei processi”.
Questa convergenza porta nelle aziende un nuovo livello di collaborazione tra aree che hanno sempre operato in modo distaccato, segnando il passaggio verso la trasformazione digitale dell’azienda.
“Ed è in questa dinamica che la meccatronica supporta la digitalizzazione, passando da una progettazione tradizionale sequenziale a una progettazione di tipo sistemico, multidisciplinare con un’ampia collaborazione tra gli specialisti”, ha spiegato Cristini, sottolineando l’importanza di abbracciare questa complessità per raggiungere un nuovo vantaggio competitivo.
Digital Twin, strategico per l’innovazione
La realizzazione del digital twin è un punto cardine della trasformazione digitale del mondo manifatturiero per la virtualizzazione della progettazione sia del prodotto sia del processo.
Il digital twin, dunque, come strategia di innovazione non solo per la progettazione dei macchinari, ma anche per gli aspetti di commercializzazione delle macchine, per esempio per esporre a un potenziale cliente le potenzialità del macchinario simulando tipologie di produzioni differenti, prestazioni e lavorazioni prima di testarle in campo.
E ancora, il digital twin sul fronte dei servizi in termini di utilizzazione, gestione e manutenzione durante tutto il ciclo di vita della macchina.
Digitalizzazione e sostenibilità: i focus per le aziende industriali
L’Italia è a tutt’oggi la seconda manifattura in Europa, in questo momento si sta registrando il tasso di occupazione più alto degli ultimi tempi e non ultimo, con il reshoring, si sta riportando in casa la produzione di importanti aziende.
Tuttavia, il riaffacciarsi dell’inflazione che non esisteva più da anni sta portando a un cambio di atteggiamento da parte del consumatore. Si sta andando verso un calo di ordinativi e conseguentemente di produzione in quasi tutti i comparti. E, in tutto questo si stanno anche ridisegnando le filiere produttive.
L’altro importante fenomeno che influenzerà pesantemente il settore industriale è quello della sostenibilità, imprescindibile per combattere il cambiamento climatico e salvaguardare il nostro pianeta.
“L’83% dei governi ha dichiarato l’impegno a ridurre le emissioni nocive e l’80% dei consumatori ha inserito il tema sostenibilità tra le proprie scelte di acquisto”, ha affermato Fabio Massimo Marchetti, Presidente Area Digitalizzazione dei Processi e dei Prodotti di Anie Automazione.
“La sostenibilità nell’industria diventa, dunque, un elemento fondamentale, ma affinché si possano realizzare prodotti e processi produttivi sostenibili serve la leva abilitante del digitale”.
Digitalizzazione e sostenibilità sono, quindi, i due focus assoluti per l’evoluzione delle imprese industriali.
Automazione Industriale: un mercato effervescente
Il mercato dell’Automazione Industriale non è solo in evoluzione, ma anche “effervescente”, come l’ha definito il presidente di Anie Automazione Andrea Bianchi.
“Il 2022 si è chiuso con una crescita del 23% per un valore che ha sfiorato i 7 miliardi di euro e, nonostante lo scenario macroeconomico globale non roseo, con l’inflazione, la difficoltà a reperire componenti elettronici e materie prime e le tensioni geopolitiche, le attese per il 2023 indicano una crescita sempre a doppia cifra, intorno al 16%”, ha affermato Bianchi.
“È anche vero che dopo anni di crescita significativa, ci troveremo, nel prossimo, ad affrontare un periodo più incerto, tuttavia la trasformazione in atto verso l’Industria 5.0 e le prospettive di agevolazioni fiscali contenute nel futuro piano Transizione 5.0 ci confortano”.
Dalle anticipazioni di Raffaele Spallone del Ministero delle imprese del Made in Italy (Mimit) - intervenuto al Forum Industria Digitale - si parla di incentivi del 40% per investimenti fino a 30 milioni di euro. Il provvedimento, ancor in fase di discussione a livello di Commessione Europea, conferma l’importanza dei Piani Transizione 4.0 e 5.0 quali strumenti essenziali per compiere la transizione gemella digitale-green.