L’automazione è una soluzione da tempo esplorata da parte delle aziende del settore automotive, sia per l’alta concorrenza che lo contraddistingue, sia per la ciclicità che ne ha segnato l’andamento negli ultimi 10 anni. In entrambi gli scenari, la robotica si è dimostrata una soluzione ottimale per ridurre i costi, aumentare la redditività e incrementare la qualità dei prodotti.
Vitesco technologies Italy, branch italiana della multinazionale tedesca, ha introdotto l’automazione in maniera spinta in molte linee produttive per assicurarsi una maggiore competitività. Negli stabilimenti di Fauglia e San Piero a Grado, in provincia di Pisa, vengono assemblati numerosi componenti essenziali per i moderni motori endotermici, come iniettori, valvole OGR, sistemi per la rigenerazione dei filtri antiparticolato dei motori diesel.
L'azienda, che fonda i propri progetti di automazione su attente analisi condotte secondo i dettami dalla lean manufacturing e del work cell design, ha deciso di introdurre in fabbrica 24 cobot Universal Robots di diverse taglie, per automatizzare le lavorazioni a minor valore aggiunto e garantirsi, al tempo stesso, una più elevata qualità dei prodotti.
I cobot UR entrano in gioco in 4 diverse applicazioni di assemblaggio e pallettizzazione:
- assemblaggio del DDU (un componente chiave per la rigenerazione del filtro antiparticolato)
- assemblaggio RDU (Reduction Dosing Unit, un iniettore che inserisce un agente riducente per abbattere gli ossidi d’azoto nei catalizzatori)
- assemblaggio Fuel Rail (un componente chiave nei motori diesel con un elevata complessità di assemblaggio)
- pallettizazione su tray metallico delle armature, componenti che entrano in gioco negli assemblaggi successivi.
Assemblaggio DDU, cella collaborativa con settimo asse
La linea di assemblaggio DDU ha un tempo ciclo di 30” e impiega un cobot UR5e (5 kg di capacità di carico e 1,5 m di diametro operativo) installato su un asse orizzontale montato a soffitto e altri 3 UR5e in una stazione adiacente con ciclo in linea. L’integrazione con l’asse lineare amplifica la flessibilità del cobot fornendogli un grado di libertà extra e una maggiore area operativa, pur conservando sicurezza e dimensioni compatte. Il cobot installato su settimo asse carica i componenti da assemblare nella stazione e scarica il prodotto finito al termine del ciclo di assemblaggio.
Il secondo cobot UR5e, dislocato nella cella adiacente, ha il compito di applicare un dispositivo di tenuta sul componente. In questo caso, l’uso del cobot conferisce flessibilità e sicurezza all’applicazione, consentendo di tenere la cella aperta e permettendo agli operatori di interagire con il processo produttivo e di effettuare gli interventi manutentivi necessari.
Il terzo e il quarto cobot hanno invece il compito di applicare un lubrificante sul prodotto finito e di movimentare alcune telecamere per il controllo di processo, verificando la presenza di tutti i componenti tramite protocolli di intelligenza artificiale.
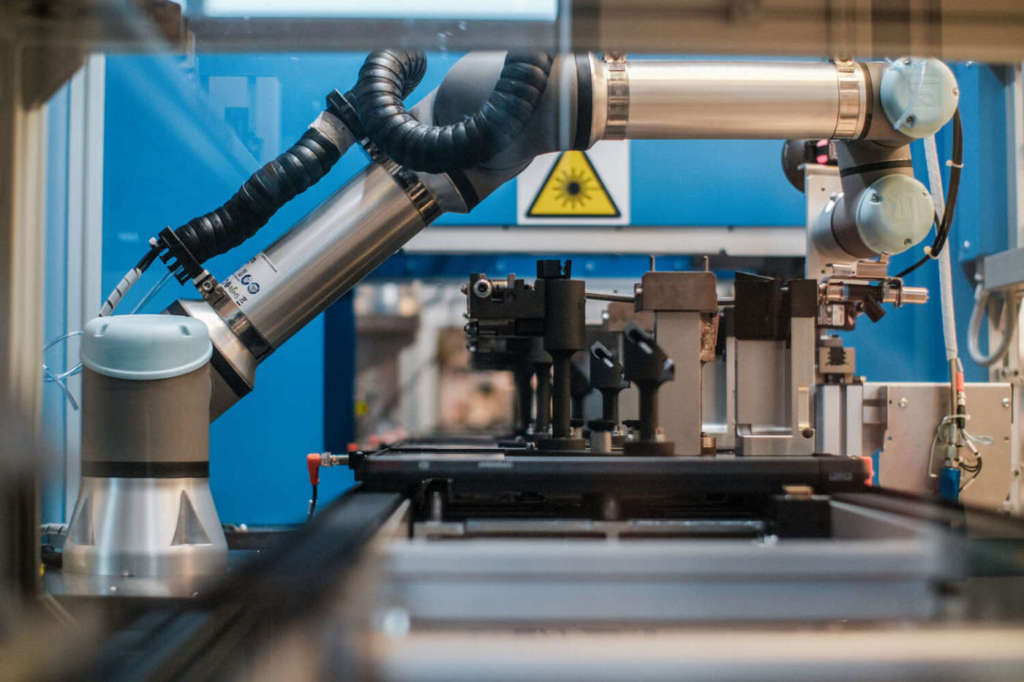
Assemblaggio RDU, flessibilità e collaborazione
Per abbattere le emissioni inquinanti i moderni motori diesel utilizzano i catalizzatori SCR (Selective Catalyst Reduction). Si tratta del catalizzatore a riduzione selettiva, un componente dell’auto che abbatte le emissioni di ossidi di azoto. Ciò grazie all’impiego di un agente riducente, il quale viene iniettato attraverso il Reduction Dosing Unit (RDU).
I cobot UR (5 modelli UR5) sono stati integrati nella linea di assemblaggio degli RDU nell’operazione di applicazione di un componente protettivo in gomma sui tubi dell’RDU. Il design del prodotto contiene un ampio range di tolleranze relative all’assemblaggio di diversi sottocomponenti. Per questo motivo, è necessaria alta flessibilità di inserimento durante l’operazione. Inoltre, per garantire la movimentazione di cappellotti di vario diametro, il gripper del cobot ha capacità adattative e un controllo sul carico di presa per assicurare la giusta reazione durante l’inserimento in forza.
L’applicazione ha permesso di eliminare le operazioni manuali, andando a migliorare anche l’efficienza della linea stessa.
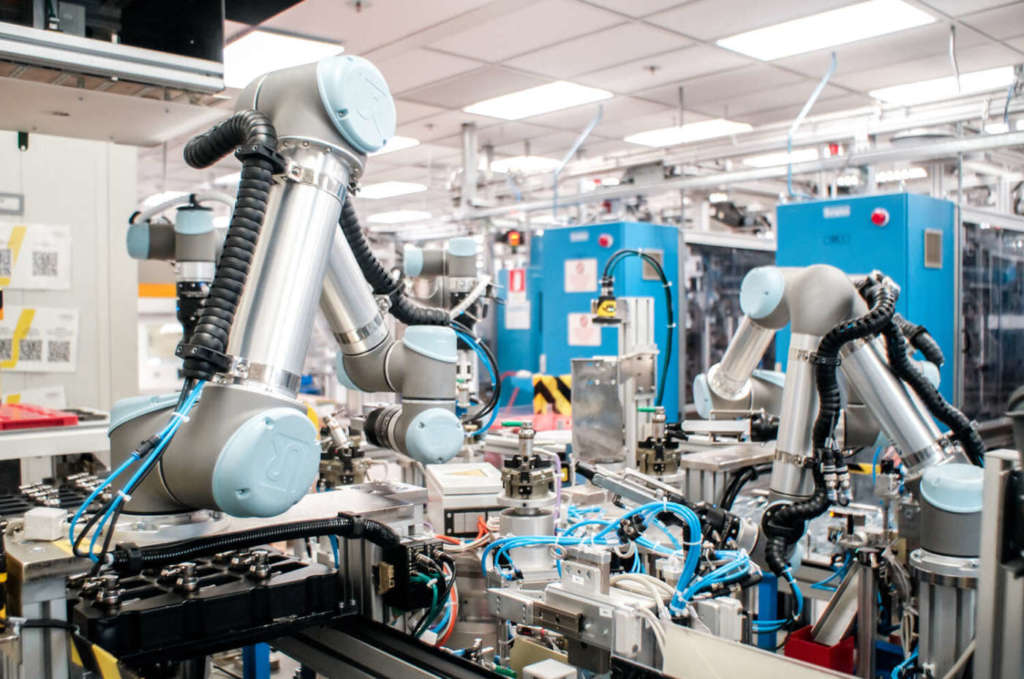
Assemblaggio Fuel Rail: + 70% ergonomia, - 11% tempo ciclo
L’integrazione dei cobot nella linea di assemblaggio del fuel rail ha permesso una riduzione dell’11% del tempo tasso ergonomico.
Nella linea di assemblaggio, 10 cobot UR10 (10 kg di payload per 2,6 m di diametro operativo) dislocati a coppie su cinque linee identiche giocano un ruolo chiave. UR10 è il secondo cobot più grande della gamma di UR, capace di offrire un’ampia portata operativa e di asservire diverse macchine da un’unica stazione.
I cobot sono chiamati ad automatizzare il processo di carico e scarico del componente che era precedentemente eseguito in maniera manuale, e sono stati introdotti in linea senza apportare sostanziali modifiche al layout e alla struttura della produzione.
Tale risultato è stato possibile grazie alla collaboratività offerta dai cobot e alle safety native che ne permettono l’integrazione anche in assenza di barriere di recinzione (previa analisi del rischio, ovviamente).
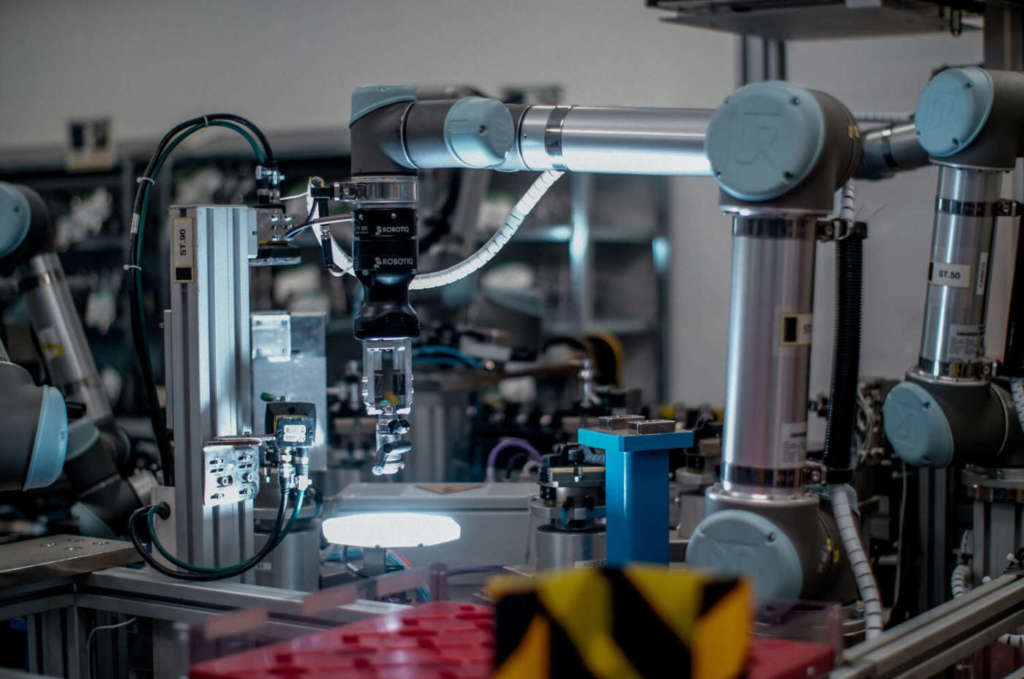
Pallettizzazione armature: cella compatta, flessibile e spostabile
Grazie all’utilizzo di un cobot UR3 (3 kg di payload e 500 mm di sbraccio operativo), Vitesco Technologies Italy ha sollevato un operatore da un lavoro usurante e ripetitivo: la pallettizzazione delle armature su un tray metallico. In questa applicazione, un nastro trasporta i componenti (le armature) fino a un singolarizzatore, il quale li posiziona nel punto di prelievo attraverso un asse elettrico che si muove parallelo alla direzione di avanzamento, e un asse pneumatico che si muove perpendicolarmente al nastro.
Quando le armature si trovano nella posizione di prelievo, il cobot UR3 preleva due pezzi alla volta attraverso un doppio gripper e li pallettizza in un tray metallico. Poi, il cobot preleva con una doppia pinza due componenti per volta, lasciando inalterato il parametro di produttività.
Un aspetto cruciale su cui l’azienda si è focalizzata è la flessibilità. Infatti, con delle modifiche al gripper e al sistema di singolarizzazione, è stato possibile gestire e pallettizzare componenti diversi rendendo l’applicazione versatile. Inoltre, la cella – un’isola compatta montata su ruote – può essere spostata in zone diverse dell’area produttiva dando origine a nuove applicazioni.
I vantaggi dell’automazione collaborativa
Grazie all’implementazione dei cobot Universal Robots all’interno delle proprie linee, Vitesco Technologies Italy è riuscita a migliorare notevolmente il tasso ergonomico dei processi interni. In particolare, l’esecuzione di alcuni complessi task di assemblaggio, prima eseguiti manualmente, ha consentito all’azienda di dislocare i propri operatori su attività a maggior valore aggiunto.
In secondo luogo, l’azienda ha potuto beneficiare della flessibilità e collaboratività dei cobot UR: i cobot, infatti, operano principalmente in celle di lavoro aperte all’interno delle quali gli operatori possono intervenire in caso di bisogno.
Le safety native permettono un uso flessibile (previa analisi del rischio) dei cobot, che quindi possono essere dislocati in maniera variabile a seconda del bisogno produttivo e non richiedono onerosi interventi di messa in sicurezza.
Infine, alcuni processi hanno fatto registrare una significativa riduzione dei tempi ciclo con conseguente maggior guadagno di produttività.